Glenn Schulz
Since 2011, FDT has collaborated with the OPC Foundation on the interoperability of existing off-the-shelf products. It aims to help factories and other industrial facilities to achieve higher returns in the use of open standards. . This collaboration opens the door to gaining interoperability from the sensor to the cloud across the enterprise and enhancing the lifecycle management of the entire industrial sector (see Figure 1).
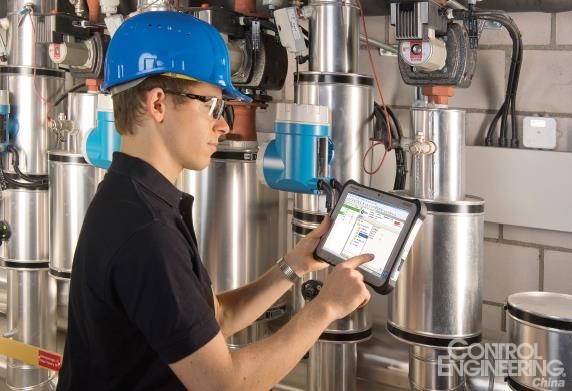
Fig. 1: The cooperation between the FDT organization and the OPC Foundation opens the door for companies to gain interoperability from the sensor to the cloud and enhance the lifecycle management of the entire industrial sector. Image Source: FDT Organization
Establish open standards
To understand the current development of the FDT and OPC standards in full swing and the benefits they can provide in process and factory automation, a brief review of their historical development is needed.
The FDT standard began in 1998 and was successively absorbed into the IEC 62453, ISA103, and China GB/T 29618 standards. It is dedicated to providing an open, vendor-neutral communication and configuration interface between field devices and host systems. This includes a general-purpose environment for accessing the complex functions of the device (see Figure 2).
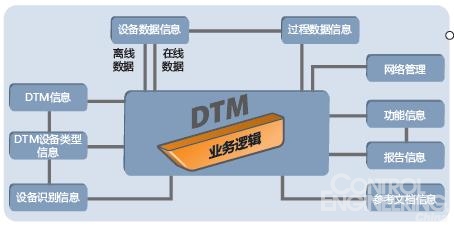
Figure 2: The FDT standard provides an open, vendor-neutral communication and configuration interface between the field device and the host system, which includes a common environment for accessing the complex functions of the device.
The standard has two main software parts: one is a frame application including a graphical user interface (GUI) (FDT/framework); the other is a device type manager (DTM), which is a device driver and provides a manufacturer Given control of the properties displayed by the device. The framework application can be embedded in programmable logic controller (PLC) programming tools, distributed control systems (DCS) and asset management systems, or used as a stand-alone configuration tool. The new version of FDT2.0 can support the latest operating environment and uses the Microsoft .NET technology platform.
The OPC standard began in 1996 and aims to achieve safe and reliable data exchange in manufacturing plants and other companies. The OPC Unified Architecture (OPC UA) is a platform-independent, service-oriented architecture and integrates the original technical specifications of OPC under the same framework.
The FDT standard is intended to be an important information hub, while the OPC UA standard provides the infrastructure to make information available for other applications and platforms. The two work together to enable sensor, network, and topology information to be provided to Enterprise Resource Planning (ERP) systems, Cloud, Industrial Internet of Things (IIoT), and Industry 4.0.
Increase the interoperability of existing products
The idea behind the FDT/OPC joint project is to provide a standard plug-in for the FDT 2.0 standard so that it can use the OPC UA specification to provide connectivity for enabling data communications throughout the enterprise. This approach fully embodies the device-to-cloud computing strategy, which can provide features such as configuration, diagnostics, device health, communications, historical data access, and alarm and event services for existing and future FDT-enabled devices.
The FDT standard uses physical network topologies and logical topologies to implement factory tiering. Network protocols in an industrial environment allow the framework application system to talk to any device. This includes the ability to access terminal devices through transparent channels of different networks. Framework applications can also receive debugging, diagnostics, predictions, and other high-level data during the operational lifecycle. To make these data sources available for use by the OPC UA architecture, the data is mapped into the OPC UA data model, and the system supporting the FDT/framework is configured as an OPC UA server (see Figure 3).
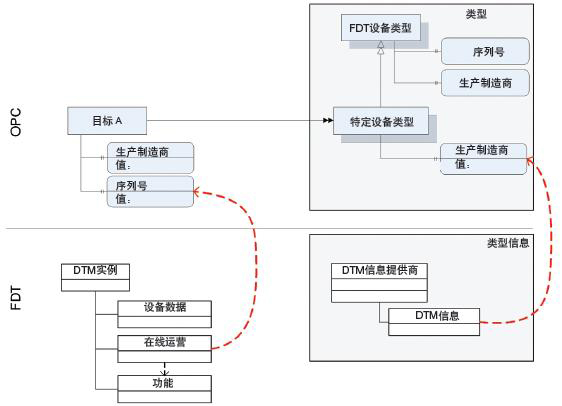
Figure 3: Mapping of device type information.
The client can request a secure connection with the FDT/OPC server and access topology, health, and other data. There is no limit to the number of client accesses, but only limited by the server's capacity and network bandwidth.
Optimize network and device management
System vendors can use server-assisted devices for deployment. Embedding the framework application into the DCS, PLC, or other system vendor provides the ability to integrate the OPC UA server into an application so that it can be accessed from any client.
Integrating the information provided by the Device Type Manager (DTM) and incorporating other device drivers into the information model is an important function for device diagnostics, configuration, remote asset management, and integration with the Manufacturing Execution System (MES). The information model is designed to improve network functions and device management, which helps to optimize the enterprise by accessing data without having to deal with protocols. It also provides support for devices that were not previously supported.
The network and equipment can be configured using commonly used engineering tools such as DTMs or other devices such as Electronic Device Descriptions (EDD) and Field Device Integration (FDI) device packs. The information provided by the DTM, including device type, parameters, and input/output (I/O), can help establish the information model. The collaboration aims to increase the richness of the information model while taking full advantage of the server. In an automation architecture, servers are everywhere and used primarily for transmission and routing information.
The device communication method and machine data using the industrial device information model are designed to integrate local control and monitoring using global views and integration. This is a good example of a big data application because it allows better and faster decision making.
Control network connectivity
Frame appliaction, which has access to all control networks within the facility and all devices connected to the network. It also has full knowledge of the control network topology. The OPC UA server within the framework application enables any client application to browse the control topology and select any instrument on the network to obtain critical information about the device. Framework applications are automatically routed throughout the entire network and can bypass congested segments and connect directly to clients (see Figure 4).
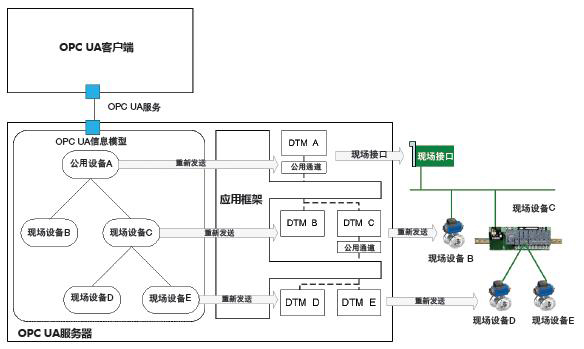
Figure 4: The OPC UA server within the FDT/framework application enables any client application to browse the topology of the control structure and select any instrument on the network in order to obtain key information about the device.
Any existing commercial OPC UA client with appropriate security rights can access the server embedded in the framework application. There are many applications for similar concepts. A maintenance technician, if he or she has installed a mobile app based on Android or an iOS device, can apply the mobile device to the factory floor to gain access to key device information. For the operating personnel, it seems that without any custom code or other applications, the wireless device can be directly connected to the assets, all this may be due to the convenience of the interface.
"The OPC UA interface provides for allowing access to device data from higher-level systems such as asset management systems."
Independence of the future platform
Auxiliary devices provide sensor-to-cloud and enterprise-wide data communications to meet the expectations of industrial end-users - leveraging the benefits of Industrial Internet of Things (IIoT) and Industry 4.0. FDT hopes to go further, establish IIoT solutions, support mobility, online security and interoperability, and be able to deploy on a stand-alone client/server or cloud architecture independently of the platform.
The combination of FDT/OPC standards aims to create a system infrastructure consisting of standardized industrial networks, automation systems and device connections. Remote access to connected machines, production devices, and equipment helps drive performance improvements. This method helps to unify the implementation and configuration of system engineering, and provides support for device diagnostics in Industry 4.0, and establishes a bridge to connect with Industry 3.0 networks and devices.
The purpose of technical cooperation is to ensure the seamless exchange of online data between automation systems, asset management systems and other factory enterprise systems and applications. This design is designed to help industrial end-users use data and information models, as well as modeling and corresponding services, to achieve integration from applications to devices.
Solid-state Capacitors / Motor Starting Capacitors
Solid - state capacitors are all called: solid - state Aluminum Electrolytic Capacitors.It with the ordinary capacitance (that is, the liquid aluminum electrolytic capacitors) the biggest difference is that use different dielectric material, liquid aluminum capacitor dielectric material as the electrolyte, and solid-state capacitor dielectric material is conductive polymer materials.Solid-state capacitors / Motor starting capacitors
Solid-state capacitors / Motor starting capacitors,Solid-State Capacitors,Solid-State Small Size Capacitors,Solid-State Low Impedance Capacitors,Long Life Solid-State Capacitors
YANGZHOU POSITIONING TECH CO., LTD. , https://www.cnpositioning.com