Welding robots are industrial robots that are engaged in welding, including cutting and painting. According to the definition of a standard welding robot by the International Organization for Standardization (ISO), an industrial robot is a versatile, reprogrammable Manipulator with three or more programmable axes for Industrial automation field. In order to adapt to different purposes, the mechanical interface of the last axis of the robot, usually a connecting flange, can be fitted with different tools or end effectors. The welding robot is to attach a welding tong or a welding (cutting) gun to the end shaft flange of an industrial robot, so that it can be welded, cut or thermally sprayed.
Second, the development history of welding robotsSince the world's first industrial robot, UNIMATE, was born in the United States in 1959, the application and development of robots has gone through three phases:
The first generation is a teaching reproduction robot. Such robots are simple to operate, do not have the feedback capability of external information, and are difficult to adapt to changes in the working environment, and their application in modern industrial production is greatly limited.
The second generation is a robot with perceptual capabilities. Such robots have a certain ability to perceive the external environment, and have functions such as hearing, vision, and touch. When working, the information obtained by the sensors is used to flexibly adjust the working state to ensure that the work is completed in adapting to the environment.
The third generation is an intelligent robot. These robots not only have sensory ability, but also have the ability of independent judgment, action, memory, reasoning and decision-making. They can adapt to external objects and work in harmony, and can complete more complex actions. Intelligent robots also have fault self-diagnosis and repair capabilities. .
Welding robots are industrial robots that replace welders in welding operations in the field of welding production. Early welding robots lacked "flexibility", welding paths and welding parameters had to be pre-set according to actual operating conditions, and there were significant disadvantages in operation. With the development of computer control technology, artificial intelligence technology and network control technology, the welding robot has also evolved from a single stand-alone teaching reproduction type to a multi-sensing and intelligent flexible processing unit (system) with intelligence as the core.
Spot welding is not very demanding on welding robots. Because spot welding only requires point control, there is no strict requirement for the movement path of the welding tongs between points. This is the reason why robots can only be used for spot welding at the earliest. The spot welding robot not only needs to have sufficient load capacity, but also has a fast speed when moving between points, and the movement should be smooth and the positioning should be accurate to reduce the shift time and improve the work efficiency. How much load capacity a spot welding robot needs depends on the type of welding tongs used. For welding tongs separated from the transformer, a robot with a load of 30 to 45 kg is sufficient. However, on the one hand, the welding tongs have large electrical energy loss due to the length of the secondary cable, and are also disadvantageous for the robot to extend the welding tongs into the workpiece. On the other hand, the cable runs without the robot moving, and the cable is damaged quickly. .
Therefore, the use of integrated welding tongs is gradually increasing. This welding tongs together with the transformer quality is around 70kg. Considering that the robot has sufficient load capacity, the welding tongs can be sent to a space position for welding with a large acceleration, and a heavy-duty robot with a load of 100 to 150 kg is generally selected. In order to meet the requirements of short-distance rapid displacement of welding tongs during continuous spot welding. The new heavy-duty robot adds the ability to perform 50mm displacement in 0.3s. This puts higher demands on the performance of the motor, the operation speed of the microcomputer and the algorithm.
1) Stabilizing and improving the quality of welding, which can reflect the quality of welding in the form of numerical values;
2) Improve labor productivity;
3) Improve the labor intensity of workers and work in harmful environments;
4) Reduce the requirements for workers' operating technology;
5) Shorten the preparation period for product modification and reduce the corresponding equipment investment.
Fifth, the system composition of the welding robotWelding robots mainly include two parts: robots and welding equipment. The robot consists of a robot body and a control cabinet (hardware and software). For welding equipment, for example, arc welding and spot welding are composed of welding power source (including its control system), wire feeder (arc welding), and welding torch (clamp). For intelligent robots, there should also be sensing systems such as laser or camera sensors and their controls. Figures 1a and b show the basic components of an arc welding robot and a spot welding robot.
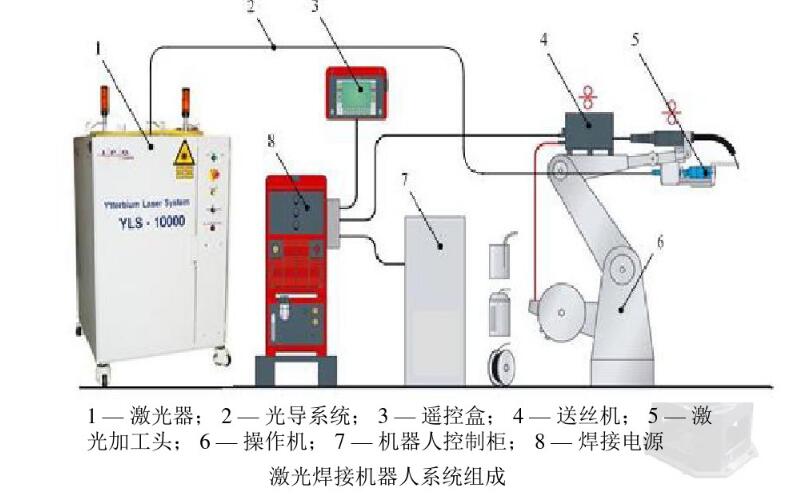
Because the designed welding robot works in a quasi-planar and narrow space environment, in order to ensure that the robot can track the weld automatically according to the deviation information of the arc sensor, the designed robot should be compact, flexible and stable. In this paper, a small mobile welding robot is developed for the characteristics of narrow space. According to the motion characteristics of each structure of the robot, the robotic mechanism is divided into three parts: the wheeled mobile platform, the welding torch adjustment mechanism and the arc sensor. Among them, the wheeled mobile platform has large inertia and slow response, mainly for rough tracking of the weld seam, the welding torch adjustment mechanism is responsible for precise tracking of the weld seam, and the arc sensor completes the real-time identification of the weld deviation. In addition, the robot controller and motor driver are integrated on the robot mobile platform to make it smaller. At the same time, in order to reduce the impact of dust on moving parts in a harsh welding environment, a fully enclosed structure is adopted to improve the reliability of the system.
The programming method of the welding robot is still based on the online teaching method (Teach-in), but the interface of the programmer has been improved a lot compared with the past, especially the adoption of the liquid crystal graphic display makes the programming interface of the new welding robot more. It is friendly and easy to operate. However, the coordinate position of the key points on the weld trajectory during robot programming must still be obtained by teaching and then stored in the motion command of the program. For some complex shape weld trajectories, it takes a lot of time to teach, which reduces the efficiency of the robot and increases the labor intensity of the programmer. There are two methods currently being solved:
First, the teaching programming only roughly obtains several key points on several weld trajectories, and then automatically tracks the actual weld trajectory by welding the robot's visual sensor (usually an arc sensor or a laser vision sensor). Although this method is still inseparable from teaching programming, it can reduce the intensity of teaching programming and improve programming efficiency to a certain extent. However, due to the characteristics of arc welding itself, the robot's vision sensor is not suitable for all weld forms.
The second is to adopt a completely off-line programming method, so that the preparation of the robot welding program, the acquisition of the coordinate position of the weld trajectory, and the debugging of the program are all completed independently on one computer, without the participation of the robot itself. Off-line programming of robots existed many years ago, but because of the limitations of computer performance at that time, offline programming software is mainly text-based. Programmers need to be familiar with all the command systems and syntax of robots, and also know how to determine the space of weld trajectories. Position coordinates, so programming is not easy and time-saving. With the improvement of computer performance and the development of computer 3D graphics technology, most of the offline programming systems of today's robots can be run in a three-dimensional graphics environment. The programming interface is friendly and convenient. Moreover, the coordinate position of the weld bead can usually be used as a virtual representation. ""virtual Teach-in" method, you can easily click the welding part of the workpiece in the 3D virtual environment with the mouse to obtain the spatial coordinates of the point; in some systems, the weld position can be directly defined by the CAD graphic file. A weld trajectory is generated and the robot program is automatically generated and downloaded to the robot control system. Thereby greatly improving the programming efficiency of the robot and reducing the labor intensity of the programmer. At present, there are offline programming software for commercial robots based on ordinary PCs in the international market. Such as Workspace5, RobotStudio, etc. Figure 9 shows the PC-based 3D visualization robot offline programming system developed by the author. The system can be used for offline programming of ABB's IRB140 robot. The weld trajectory in the program is obtained through virtual teaching, and in the three-dimensional graphics environment, the robot can simulate the movement according to the trajectory in the program to verify its accuracy and rationality. The programmed program can be downloaded directly to the robot controller via the network.
Welding robots play an extremely important role in high-quality, high-efficiency welding production. The research, development and application of industrial robot technology have strongly promoted the advancement of industrial technology in the world. In recent years, the research and application of welding robot technology has achieved many outstanding results in weld seam tracking, information sensing, off-line programming and path planning, intelligent control, power supply technology, simulation technology, welding process, and remote welding technology. With the continuous development of computer technology, network technology, intelligent control technology, artificial intelligence theory and industrial production system, there are still many problems in the field of welding robot technology that need to be seriously studied, especially the vision control technology and fuzzy control technology of welding robots. Intelligent control technology, embedded control technology, virtual reality technology, network control technology and other aspects will be the main direction of future research.
Laptop power adapter charger for HP:
Laptop Brand
Power Adapter
EliteBook 8440p 6530b
18.5v 3.5a, 7450
Compaq 6500b 6530b 6535b 6700b 6730b 6735b 6736b
19v 4.74a, 7450
Pavilion DV4 DV5 DV6-1000 CQ60 CQ61
18.5v 3.5a, 7450
COMPAQ Mini
19v 1.58a, 4017
2710p 2730p 2740p 2740w 2760p
18.5v 3.5a, 7450
Pavilion DV4 DV5 DV5T DV6 G50 G60 G70 HDX16
18.5v 3.5a, 7450
dm4-1000 Dm4t-1000 Dm4t-1100 DV3-4000 CQ42
18.5v 3.5a, 7450
Compaq Presario CQ42 CQ57 CQ72 CQ56 CQ32 CQ32-101TX I84C
18.5v 3.5a, 7450
G62 Compaq Presario CQ42 CQ72 CQ62 CQ56 CQ32 593555-001 DM4
18.5v 3.5a, 7450
DV4 DV5 DV6-1000 DV6-1200 DV6-1300
18.5v 3.5a, 7450
DV4 SPARE
18.5v 3.5a, 7450
dv4-1120us dv4-1200 dv6-2150us dv6-2155dx dv6-1245dx
18.5v 3.5a, 7450
Pavilion DV1000 DV1100 D1200 DV1300
18.5v 3.5a, 4817
DV1000 M2000
18.5v 3.5a, 4817
EliteBook 2730p 2740 2760p Compaq 2710p nc6320
18.5v 3.5a, 7450
Compaq 320 321 325 326 420 620 621 421
19v 4.74a, 4817
Pavilion dv4000 dv4100 dv4300 dv4400
19v 4.74a, 4817
Compaq DV1000 G3000 G5000
18.5v 3.5a, 4817
dv4-5000 dv6-7000 dv7-7099
19v 4.74a, 4817
dv6-7200 dv7-7200 DV4-5000 DV7-7000
19v 4.74a, 4817
DV4 DV6 CQ60 CQ70 G50 G70
18.5v 3.5a, 7450
ProBook 4340s 4341s
19v 4.74a, 7450
Pavilion DV3
19v 4.74a, 7450
ProBook 4320s 4321s 4325s 4420s 4425s 4525s
18.5v 3.5a, 7450
dv2000 dv6400 dv6700 dv6800 dv6900 A900 V6400
18.5v 3.5a, 4817
Compaq 420 421 425 4320t 620 625 320 321 325 326 621
18.5v 3.5a, 7450
ProBook 6440b 6445b 6450b 6540b 6545b 6550b 6555b
19v 4.74a, 7450
Pavillion DV7
19.5v 4.62a, 7450
G42 G72 G32 DV7-4000 DV6-6000 DV5-2000
19.5v 4.62a, 7450
Presario CQ32 CQ42 CQ43 CQ56 CQ62 CQ72
19v 4.74a, 7450
Pavilion DV6 DV6-3000 DM4-1000 Envy 15 17 G4 G6 G7-1000
19.5v 4.62a, 7450
avilion dm3 dm3-dm3t-1000 CTO dm3-1000 dv4-3100
19.5v 3.33a, 4817
DV4 DV5 G50 G60 G61 G70 G71 HDX16
19v 4.74a, 7450
CQ40 CQ50 CQ60 CQ61 CQ70 CQ71 DV4
19v 4.74a, 7450
CQ60 CQ61 CQ40 CQ41 CQ45 CQ60 G60 G70
19v 4.74a, 7450
Pavilion dm3 CTO dm3-1000 dv4-3100
19v 4.74a, 7450
Compaq 6520 6520P 6520S 515 516
19v 4.74a, 7450
2000-425NR
19v 4.74a, 7450
Our service:
Stable output and high charging efficiency.
Elegant outlook design as original one, touch smoothly and comfortable.
Original charger is good, but as a replacement, our product has more reasonable price when your original charger is broken.
And, the market of the replacement adapters becomes bigger and bigger. People would rather buy a copy one then the original because of the price.
But at the same time, people worry about that they will buy something defective. So the problem comes, how to buy a good quality one with a good price?
As a professional power adapter manufacturer, we have excellent R&D team, skilled staffs and responsible after-sale service. All your benefits can be under protected after you buy products for our company.
Our certificates :ISO9001:2008 & ISO14001:2004 , CCC , CE , FCC , ROHS.
All our products has 1 year warranty. In other words, if you get the dad products which are not damaged physically from us in one year, we will replace you the new one or the whole bulk order.
Laptop Adapter For Hp,Hp Laptop Adapter,Charger For Hp,Power Supply For Hp
Shenzhen Waweis Technology Co., Ltd. , https://www.waweisasdapter.com